/ Calidad /
Quality is one of our priorities
Download copies our certification:
Quality is one of the cornerstones of Olmar’s manufacturing process. Every piece of equipment manufactured by the company is subjected to strict checks, in accordance with the most stringent international standards, as well as those carried out by our suppliers and recorded in the respective quality control records, in compliance with the different national and international codes and regulations.
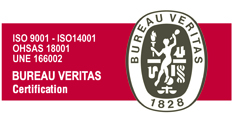
Projects subsidised by:

Projects
Objective: The project focuses on research into the coating and additive manufacturing technology called Cold Spray Additive Manufacturing (CSAM), with the aim of understanding how process parameters should be adjusted based on the substrate and filler material, and what tests should be conducted on the raw materials (powder and substrate) as well as the fabricated material to ensure its optimal performance.
PROJECT FUNDED BY:
Olmar worked on a project to standardise the system for closing autoclaves using davit arm doors. This project was funded by the Government of the Principality of Asturias and the European Union through the ERDF, as part of the Technology Innovation Voucher Programme 2014.
This project was aimed at developing a process to recover nitrogen in high-capacity industrial autoclaves. It was also subsidised by the Government of the Principality of Asturias and the EU, as part of the Innova 2014 Programme.
Olmar carried out a project to replace conventional lighting with LEDs, which was subsidised by the EU and the Principality of Asturias, in the context of energy efficiency and using renewable energies in 2014.
The aim of this project was to develop a three-ring locking system for autoclaves and was subsidised by various entities, including the EU and the Ministry of Industry, as part of the Innoempresa Programme 2007-2013.
In line with the company’s internationalisation strategy, the main aims of the project were to strengthen the presence of our products in international markets where there were entry barriers, to increase our participation in recognised global groups, and to position ourselves as one of the two most important suppliers of autoclaves worldwide in the aerospace and aeronautics sector.
Funded by the ERDF and the Principality of Asturias, Olmar developed an autoclave for testing to enable manufacturers of carbon fibre parts to optimise their processes and reduce energy consumption.
Industrial Olmar S.A. carried out an innovative project entitled ‘Development of a new process for recovering nitrogen in high capacity autoclaves’.
This project was funded with the support of the European Union through the ERDF and the Principality of Asturias, as part of the Science, Technology and Innovation Plan 2013-2017, under the call for proposals for the Jovellanos Programme.
Objectives of the project:
- To evaluate, select and optimise an efficient process for recovering nitrogen used in curing composite materials in large autoclaves.
- This new process was aimed at significantly reducing energy and environmental costs, while improving the operational efficiency of the facilities.
This project was funded by IDEPA and the EU and was aimed at ensuring the homogeneity of temperatures during the curing of composite materials, thereby optimising the process.
Olmar developed a system to analyse defects in composite materials using thermal imaging, co-funded by the Ministry of Economy and the EU, as part of the 2015 Challenges in Society project.
This aim of this project was to develop a system for designing fire-tube boilers using computational fluid dynamics (CFD) and finite element method (FEM) tools to optimise their efficiency and reduce the consumption of materials.
This project was funded by the Principality of Asturias through IDEPA and the European Union through ERDF funds, as part of the 2017 Business Investment Projects Programme. The main aim was to diversify OLMAR’s operations by implementing additive manufacturing technologies. More specifically, it looked to establish a new production line based on cold spray technology, with the intention of opening up new business opportunities in the medium and long term.
Project subsidised by:
The aim of this project was to implement a new additive manufacturing methodology. This technology focused on producing and repairing tools for curing composite materials used in the aerospace industry. The project was subsidised by the Government of the Principality of Asturias and the European Union, through IDEPA and the ERDF, as part of the RIS-Enterprise Programme, under the 2017 Asturias RIS3 Strategy.
Project subsidised by:
Industrial Olmar S.A. carried out a project called “Development of an autoclave with vertical flow circulation” financed by the Government of the Principality of Asturias through IDEPA and the European Regional Development Fund (ERDF). This project was part of the Asturias RIS3 Strategy (RIS-Enterprise Programme) and was aimed at creating a vertical flow autoclave that could be adapted to the different needs of curing parts of different sizes and materials. To achieve this, the design of the equipment and the airflow regulation systems was improved, looking to achieve a more efficient, optimised operation.
Industrial Olmar S.A. carried out a project entitled “Advice on and exploration of the capabilities of additive manufacturing using laser sintering technologies on metallic materials” for the defence sector. This project was funded by the Government of the Principality of Asturias through IDEPA and the European Union (ERDF), and was aimed at applying DMLS (Direct Metal Laser Sintering) technologies to manufacture innovative components in areas such as capital goods and new products for the defence sector. The aim was to take advantage of additive manufacturing to optimise the production of these elements.
Industrial Olmar S.A. carried out a project to design a system for closing autoclaves using davit arm doors, funded by the Government of Asturias (IDEPA) and the European Union (ERDF) under the call for proposals for INNOVA IDEPA 2019. The aim was to create a more robust, optimised, precise closure system, with a design that could be customised to adjust the dimensions based on the size of the equipment and the weight of the door.
The aim of this project was to establish a continuous connection between the autoclaves and Olmar’s headquarters via the internet. It looked to implement digitalisation tools to optimise the technical and energy performance of pressure equipment.
Olmar developed a control system using dielectric analysis to monitor the curing cycle of composite materials. The aim of this project, which was also funded by the Government of Asturias and the EU, was to validate this technology in real conditions and then integrate it into the systems for monitoring commercial autoclaves for industrial use.
Olmar S.A. worked on a new process for curing composites using water vapour/steam to manufacture aerospace structural parts. This project was co-funded by the European Regional Development Fund (ERDF) and sought to innovate in the aerospace sector by improving curing techniques.
Project funded by the Science, Technology and Innovation Plan 2018-2022 of the Department of Science, Innovation and University in the Scientific Missions of the Principality of Asturias 2022 programme.
This study focused on integrating cold spray technology with direct metal laser sintering (DMLS), a significant breakthrough in manufacturing processes. The aim is to improve the quality and functionality of metal parts, underlining innovation as the key to developing new products in the sector.
Industrial Olmar S.A., which has been in business since 1945 manufacturing steam boilers and autoclaves, prioritises research, development and innovation (R&D&I) as the cornerstones of its strategy. Our company is a leader in the pressure equipment sector, distinguished by the use of advanced autoclaves. Our goal is to become a leading supplier to the aeronautics/aerospace industry. To achieve this, Olmar has implemented a sustained focus on innovation, which includes:
- Development of innovative capabilities.
- R&D&I projects for new products and services.
- Operational innovation to ensure quality control in a company.
- Commitment to sustainability and occupational health.
- Ensuring that the R&D&I management system is effective and dynamic.
Project supported by the incentive program linked to self-consumption and storage with renewable energy sources, as well as the implementation of renewable thermal systems in the residential sector within the framework of the Recovery, Transformation, and Resilience Plan, funded by the European Union – NextGenerationEU #RecoveryPlan