Autoclaves pour la vulcanisation
Les autoclaves Olmar ATV pour la vulcanisation sont principalement utilisés dans l’industrie du caoutchouc mais sont également présents dans les processus de consolidation d’autres matériaux comme l’acier ou le plastique.
L’utilisation de ces autoclaves est très répandue dans divers secteurs comme l’industrie automobile (principalement pour la vulcanisation des pneus), l’industrie navale (fabrication de protections et d’accessoires), le design de rouleaux et de tapis convoyeurs ou la vulcanisation d’éléments accessoires (tubes, tuyaux, joints, etc.). C’est grâce à cette grande variété de marchés que les autoclaves de vulcanisation Olmar ATV sont parmi les équipements les plus demandés aux niveaux national et international.
Tout le processus est entièrement automatisé grâce au nouveau logiciel Olmar OCS, totalement développé par les ingénieurs d’Olmar et qui permet de contrôler, étudier et agir sur toutes les variables du cycle en temps réel. Ce système moderne garantit un résultat final optimal et permet de réaliser divers programmes de travail, de suivi et de contrôle en fonction des différents besoins de chaque client.
- Industries
- Autres autoclaves
L’utilisation du caoutchouc vulcanisé dans les industries les plus avancées au niveau technologique s’est généralisée ces dernières années, passant d’une découverte accidentelle à une industrialisation sans précédent dans le secteur automobile au début du XXe siècle
Rappelons brièvement son histoire : une nuit de 1839, Charles Goodyear laissa du caoutchouc naturel mélangé à du soufre sur une plaque chaude ; le lendemain matin, ce caoutchouc s’était transformé en gomme élastique, après avoir effectué le premier cycle de séchage du caoutchouc de l’histoire. Ce procédé fut breveté par M. Goodyear en 1843 (également par M. Thomas Cook au Royaume-Uni, raison pour laquelle il existe plusieurs théories à propos de son invention).
Étant donné que la chaleur et le soufre sont associés au dieu Vulcain, le processus a été appelé vulcanisation.
La vulcanisation en autoclave est un procédé chimique appliqué au caoutchouc et à d’autres composés naturels avec des propriétés élastomères, qui permet de renforcer leur élasticité et de réduire leur plasticité, améliorant ainsi leurs propriétés mécaniques, physiques et de performance telles que leur dureté, leur viscosité et leur résistance (principalement à la traction et aux intempéries).
Les autoclaves de vulcanisation Olmar (ATV) permettent d’accélérer ces processus, permettant de transformer en toute sécurité et de manière optimale le caoutchouc naturel et le plastique (caoutchouc synthétique) en pièces et produits durcis.
Elles peuvent être appliquées dans d’innombrables secteurs et processus industriels ; la croissance exponentielle du caoutchouc vulcanisé en autoclave est principalement déterminée par son utilisation dans:
Produits / Autoclave pour vulcanisation de caoutchouc et gomme / Autoclaves et caoutchouc et gomme
- Le revêtement et la réparation des pneus pour véhicules lourds comme les camions et les véhicules tout-terrain (OTR - Off Road Tires).
- Le revêtement et la réparation des enveloppes de pneus de voitures de passagers (SBR - caoutchouc styrène-butadiène)
- Le revêtement de rouleaux sur les tapis convoyeurs
- Le revêtement de rouleaux dans les imprimeries
- La fabrication de joints d'étanchéité en caoutchouc pour l'automobile, l'aviation et la construction navale, de tuyaux de radiateur, de câbles et de capuchons de bougie (caoutchouc EPDM).
- Des applications électriques comme l'isolation des câbles à haute tension
- Le revêtement de câbles à haute température
- La fabrication de tuyaux et de manchons en caoutchouc à basse, moyenne et haute pression
- La fabrication de couverture de protection en caoutchouc dans laquelle la résistance thermique à l’ozone, aux intempéries, aux substances chimiques, corrosives ou huiles sont des propriétés essentielles.
- Le séchage de joints d’étanchéité et joints (O-rings).
- D'autres comme les tapis, les bottes, etc.
Ces produits améliorés par le processus de traitement en autoclave, seront utilisés dans des conditions abrasives et/ou dans des environnements extrêmement corrosifs, ce qui augmentera leur durée de vie et améliorera leur rendement. Ce résultat ne peut généralement pas être obtenu par un moulage par compression standard basé sur une presse.
Les autoclaves pour la vulcanisation du caoutchouc fabriqués par Olmar (appelés «ATV») se distinguent non seulement par leur haut niveau de développement technologique, mais également par leur fiabilité et leur durabilité, qui garantissent le meilleur rendement et les meilleurs niveaux d’efficacité tout au long de leur durée de vie utile. L’application du caoutchouc dans des éléments de fabrication de plus en plus critiques a provoqué une augmentation exponentielle des exigences des tests de contrôle, de fatigue et de mesure de ces équipements. Seuls les autoclaves les plus avancés sont capables de garantir les niveaux d’homogénéité et les cycles demandés par l’industrie ; il est par conséquent de plus en plus important d’investir en R&D et dans l’amélioration continue.
Dans ce sens, depuis le début de son activité dans ce secteur (l’entreprise a détenu la représentation d’Uniroyal pour l’Espagne pendant plus de 15 ans dans les années 70) Olmar consacre une grande partie de ses ressources et de sa R&D à la recherche sur les possibilités de ces nouveaux matériaux ; c’est une entreprise de référence aux niveaux national et international dans leur étude et leur application dans l’industrie.
Cycle pour la vulcanisation du caoutchouc
Comme nous l’avons vu, le caoutchouc est principalement un élastomère qui peut être d’origine naturelle ou synthétique (fabriqué dans les usines pétrochimiques par synthèse chimique), ensuite vulcanisé dans un autoclave pour améliorer ses propriétés physiques et structurelles.
Dans un cycle standard, une fois introduit dans l’autoclave, le caoutchouc doit atteindre une température de 170ºC (350ºF) et une pression de 6 BarG (90 psi), et rester à cette température et à cette pression pendant une durée définie à l’avance. Ces conditions peuvent varier en fonction du type de caoutchouc et de son application.
Il est essentiel de définir correctement avec le fournisseur le temps maximum dans lequel nous voulons atteindre ces conditions de température et de pression afin d’optimiser la productivité que nous attendons de notre autoclave. Ces données sont fondamentales pour comparer et aligner différents équipements et choisir le mieux adapté à notre processus.
Étant donné la variété des cycles existants pour la vulcanisation du caoutchouc, il existe un grand nombre de types d’autoclaves différents concernant :
Les autoclaves pour la vulcanisation du caoutchouc fabriqués par Olmar (appelés «ATV») se distinguent non seulement par leur haut niveau de développement technologique, mais également par leur fiabilité et leur durabilité, qui garantissent le meilleur rendement et les meilleurs niveaux d’efficacité tout au long de leur durée de vie utile. L’application du caoutchouc dans des éléments de fabrication de plus en plus critiques a provoqué une augmentation exponentielle des exigences des tests de contrôle, de fatigue et de mesure de ces équipements. Seuls les autoclaves les plus avancés sont capables de garantir les niveaux d’homogénéité et les cycles demandés par l’industrie ; il est par conséquent de plus en plus important d’investir en R&D et dans l’amélioration continue.
Dans ce sens, depuis le début de son activité dans ce secteur (l’entreprise a détenu la représentation d’Uniroyal pour l’Espagne pendant plus de 15 ans dans les années 70) Olmar consacre une grande partie de ses ressources et de sa R&D à la recherche sur les possibilités de ces nouveaux matériaux ; c’est une entreprise de référence aux niveaux national et international dans leur étude et leur application dans l’industrie.
- Dimensions: Olmar propose des autoclaves d’un diamètre Ø utile allant de 500 mm à 10 000 mm et des longueurs entre 1 000 mm et 60 000 mm.
- Températures et pressions maximales de travail (jusqu’à 482ºF) et 21 BarG (300 psi)
- Matériaux: acier au carbone, acier inoxydable ou combinaison de matériaux différents
- Disposition: horizontale ou verticale
Les phases les plus courantes à suivre pendant un cycle de vulcanisation sont les suivantes:
1/ Chauffage et pressurisation
Les moyens de chauffage et de pressurisation à utiliser à l’intérieur de l’autoclave sont conditionnés par la nature du caoutchouc à vulcaniser et par son objectif ; il existe quatre modalités principales :
- Vapeur directe : par introduction directe de vapeur saturée dans la chambre de l’autoclave (Olmar est également fabricant de référence de chaudières à vapeur, avec plus de 1 000 références dans le monde et >75 ans d’expérience). Dans ces cycles, la pressurisation peut être corrélative à la température de la vapeur ou réalisée de manière indépendante par l’introduction d’air comprimé.
- Chauffage indirect par introduction de vapeur ou d’huile thermique : dans un échangeur situé à l’intérieur de l’autoclave, en faisant recirculer l’air chaud intérieur par une turbine et son moteur. Dans ce cas, la pressurisation se fait de manière indépendante en introduisant de l’air comprimé dans l’autoclave. L’utilisation d’air chaud au lieu de vapeur permet d’éviter le contact direct du caoutchouc avec la vapeur, ce qui minimise les infiltrations d’humidité et permet d’obtenir une meilleure adhérence du caoutchouc vulcanisé.
- Chauffage indirect par résistances électriques, en faisant recirculer l’air à l’intérieur de l’autoclave avec une turbine et son moteur. Dans ce cas, la pressurisation se fait de manière indépendante en introduisant de l’air comprimé dans l’autoclave. L’utilisation d’air chaud au lieu de vapeur permet d’éviter le contact direct du caoutchouc avec la vapeur, ce qui minimise les infiltrations d’humidité et permet d’obtenir une meilleure adhérence du caoutchouc vulcanisé.
- Chauffage mixte avec vapeur directe/indirecte : un autoclave développé par Olmar pour pouvoir travailler avec le meilleur des deux technologies à tout moment, en fonction des besoins.
2 / Phase de stabilisation
Une fois ces conditions objectives atteintes (température et pression de travail), elles doivent être maintenues pendant la durée minimale établie pendant la phase de stabilisation, qui se réalise entièrement automatiquement grâce au système de contrôle OCS (Olmar Control System) équipé de la technologie PLC de Siemens ou Allen Bradley.
3/ Refroidissement
Comme dans la phase de chauffage, les moyens de chauffage et de pressurisation à utiliser à l’intérieur de l’autoclave sont conditionnés par la nature du caoutchouc à vulcaniser et par son objectif; il existe trois modalités principales :
- Refroidissement naturel : l’autoclave est refroidi naturellement au fur et à mesure que la vapeur est extraite de l’intérieur. Il est nécessaire dans certains cas de compenser cette dépressurisation en introduisant de l’air comprimé pour garantir une finition optimale du produit.
- Refroidissement par douche ou spray : l’autoclave est refroidi par de l’eau introduite depuis la partie supérieure de l’autoclave et pulvérisée sur le produit par douche ou spray.
- Refroidissement indirect : ce système est basé sur l’introduction d’eau froide dans un échangeur situé à l’intérieur de l’autoclave, en faisant recirculer l’air à l’intérieur de l’équipement avec une turbine et son moteur.
Types de cycles pour la vulcanisation de pneus
1 / Par vapeur directe
Une fois l’autoclave chargé, on introduit de la vapeur saturée sous pression pour soumettre les pneus aux conditions de température et de pression programmées.
2 / Par chauffage indirect
Dans ce type de cycle, chaque pneu est enfermé dans une « enveloppe » (revêtement en caoutchouc) qui à son tour comporte une valve par laquelle de l’air comprimé peut être introduit pour pressuriser celui-ci.
Une fois l’autoclave chargé, on relie les tuyaux aux enveloppes pour les mettre sous pression pendant le cycle.
Comme nous l’avons expliqué ci-dessus, dans ce cas, l’air chaud est obtenu grâce à la recirculation de vapeur ou d’huile thermique dans un échangeur ou encore par des résistances électriques. Lorsque la température interne atteint 125ºC (290ºF), les enveloppes disposées à l’intérieur des pneus sont gonflées et de la pression est introduite dans l’autoclave (avec une différence de 2,1 BarG (30psi), jusqu’à ce que la chambre atteigne une pression de 5,5 BarG (80 psi) et les pneus 8 BarG (115 psi).
À ce moment nous pressurisons l’enveloppe qui recouvre le pneu est ensuite pressurisée jusqu’à 4,2 BarG (60 psi) ; on appelle généralement cette pression « troisième pression » ; elle garantit un collage optimal et une meilleure finition du pneu.
Cette partie du processus dure normalement entre 120 et 150 minutes.
Une fois les étapes ci-dessus terminées, nous procédons à la dépressurisation dans l’ordre suivant :
- Troisième pression
- Pression du pneu
- Pression de l’autoclave
L'autoclave intelligent, un logiciel de contrôle révolutionnaire
La précision et la fiabilité sont des facteurs indispensables dans les procédés de fabrication du verre. En raison de l‘exigence des normes que ces pièces doivent respecter avant d’être installées dans les secteur automobile et de la construction, il est nécessaire de faire un suivi et un contrôle exhaustifs de tous les processus se déroulant à l’intérieur de l’autoclave. Olmar a dans ce sens développé le logiciel le plus avancé au monde pour les autoclaves de laminage de verre et la société atteint ainsi ses objectifs de numérisation et d’efficience dans les processus de fabrication. Les nouveaux autoclaves Olmar sont en définitive des autoclaves intelligents capables de contrôler automatiquement la pressurisation à l’air ou à l’azote, les rampes de chauffage grâce à l’utilisation de batteries électriques ou d’huile thermique à haut rendement, le maintien des valeurs de vide, de pression et de température (thermocouples) pendant le séchage, ainsi que le refroidissement et la dépressurisation ultérieurs, ce qui permet de contrôler et de paramétrer chacune des phases de fabrication. Nous pouvons ainsi obtenir un verre totalement transparent, avec des paramètres de débordement et de rétraction du PVB optimaux et toujours conformes avec les normes les plus exigeantes du marché.
Il n’est pas seulement important de contrôler et d’analyser ces valeurs (pression, vide ou température) pendant le cycle, il convient de le faire également après le cycle ; grâce à l’étude de toutes les données recueillies en cours de processus réalisé à l’intérieur de l’autoclave, il est possible de détecter d’éventuels points d’amélioration et d’optimiser le cycle au maximum. Grâce à un système de contrôle entièrement développé par l’entreprise à travers ses départements électrique et de logiciel, Olmar offre à ses clients des prestations optimisées et, grâce à sa technologie innovante de rapports, le contrôle et l’analyse de données les plus précis du marché international, en misant fermement sur le développement de « l’Industrie 4.0 » et en appliquant toutes les innovations disponibles dans ses autoclaves.
Olmar a concentré ses efforts sur la création d’un autoclave « intelligent », en axant ses développements sur les domaines de l’efficience énergétique, la facilité d’utilisation, le contrôle prédictif et une maintenance réduite.
Son logiciel de contrôle OCS comprend toutes ces fonctionnalités, réduit les coûts de consommation de l’autoclave, améliore sa productivité et optimise toutes les tâches de maintenance périodique à réaliser. Grâce à sa grande connectivité et à l’intégration des solutions les plus avancées de connexion à distance, notre service technique offre un soutient de premier ordre dans n’importe quel pays du monde.
Tout ceci englobé au sein d’une structure d’entreprise solide, de tradition familiale, à la fois souple et agile, capable d’exécuter l’ensemble du processus de fabrication « in house » ; une entreprise axée sur la recherche continue de l’innovation et la croissance. C’est ce que démontre sa nouvelle division de « Technologie additive à froid », un concept révolutionnaire né de notre investissement en R&D.
Générateurs de vapeur Olmar
Olmar est aujourd’hui leader mondial dans la fabrication d’autoclaves pour le caoutchouc. Ce leadership repose principalement sur la combinaison d’une ingénierie classique et innovante et sur une connaissance approfondie de l’autoclave et du processus
Olmar dispose également dans ce domaine d’un avantage important sur ses concurrents : ses connaissances et sa capacité de production en matière de générateurs de vapeur, avec plus de 1 000 références et 50 ans d’histoire.
Nous vous recommandons à ce sujet de visiter la section « Générateurs de vapeur » (Steam Boilers), où vous trouverez les différentes gammes de chaudières que nous fabriquons, avec des productions allant de 100 kg/h à 30 000 kg/h.
Olmar a par ailleurs la capacité d’offrir en option à ses clients une solution « clé en main » comprenant tous les systèmes auxiliaires venant compléter l’autoclave pour la vulcanisation du caoutchouc :
- Systèmes de chargement, manuels, semi-automatiques ou automatiques.
- Silencieux pour réduire les émissions sonores pendant la dépressurisation
- Hardware et capteurs pour la surveillance des processus
La possibilité de sélectionner un seul fournisseur, tant pour l’autoclave que pour ses équipements auxiliaires, facilite les communications et l’intégration de tous, ainsi qu’une plus grande probabilité de succès dans le résultat final du projet.
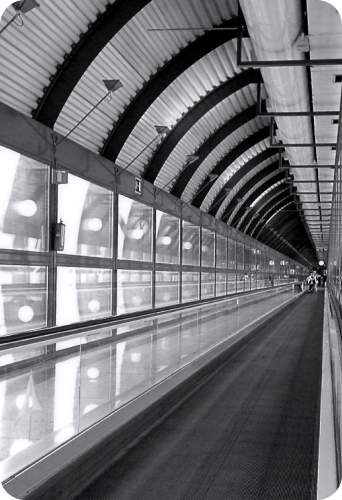
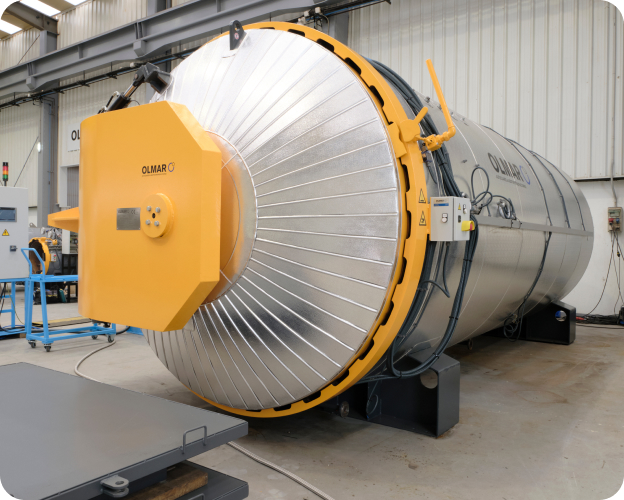
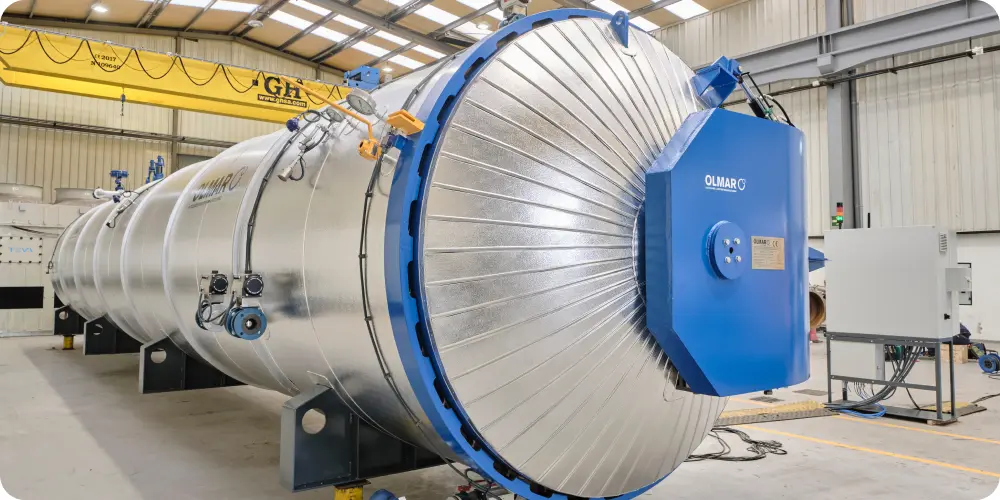
Véhicules lourds et de passagers dans le secteur de l’automobile : secteur principal dans l’utilisation d’autoclaves pour les vulcanisations de caoutchouc
L’expérience de la société, cautionnée par des milliers de références internationales et des clients de premier ordre, s’est renforcée au fil des ans en se basant sur des valeurs telles que l’excellence, l’effort et l’innovation constante. Des entreprises leaders comme Michelin, Bridgestone, Continental, Siemens ou Hutchinson, parmi beaucoup d’autres, ont fait confiance aux autoclaves Olmar pour exécuter certains de leurs projets phares, dans des produits qui offrent les solutions les plus avancées pour les secteurs de l’automobile, de l’énergie électrique, etc. La preuve en est les nombreux processus dans lesquels sont utilisés et intégrés les autoclaves et les systèmes de contrôle Olmar.
Olmar est présent dans tous ces projets et participe activement à des projets actuels et disruptifs qui révolutionneront notre avenir ; en apportant ses efforts, son excellence et son innovation dans les solutions technologiques pour la fabrication d’autoclaves pour la vulcanisation du caoutchouc encore jamais vus. Grâce à notre logiciel de contrôle qui est aujourd’hui considéré comme l’application la plus avancée pour le traitement du caoutchouc, Olmar est un fabricant de référence internationale sur un marché mondial de plus en plus compétitif.
L’augmentation de la consommation et de la production de pneumatiques est à n’en pas douter une tendance à la hausse, définissant un marché dans lequel le chiffre d’affaires individuel des grandes entreprises dépasse les 20 milliards d’euros.
Olmar est aujourd’hui le partenaire de confiance pour relever ce défi dans n’importe quel pays du monde.
Références dans le monde
La présence de plus de 1 500 autoclaves Olmar dans 150 pays est aujourd’hui la preuve de notre succès et un héritage qui est transmis de génération en génération (aujourd’hui Olmar est une entreprise familiale de quatrième génération).
Tout ce travail est accompagné des dernières certifications internationales exigées quant à la fabrication, les procédures et la qualité, avec notamment les labels CE (Europe), ASME (Amérique et Asie), SELO (Chine), JIS (Japon), etc.
Pour l'avenir, une nouvelle génération d’autoclaves
Dans ce scénario prometteur de croissance et de nouveaux défis, Olmar se renforce comme société de référence mondiale en présentant ses équipements et ses solutions technologiques comme une garantie de qualité et d’efficacité maximales pour relever les défis de l’industrie dans les années à venir. Grâce à l’expérience acquise pendant ses plus de 75 ans d’histoire et à son équipe de techniciens experts hautement qualifiés, la société affronte ces nouveaux défis avec la sécurité et la confiance nécessaires pour répondre aux besoins de ses clients dans le monde entier.
Tout ce travail est accompagné des dernières certifications internationales exigées quant à la fabrication, les procédures et la qualité, avec notamment les labels CE (Europe), ASME (Amérique et Asie), SELO (Chine), JIS (Japon), etc.