Autoklaven für die Vulkanisation
Die Olmar-Autoklaven ATV für die Vulkanisation werden hauptsächlich in der Kautschukindustrie eingesetzt, finden aber auch bei der Verfestigung anderer Materialien wie Stahl oder Kunststoff Verwendung.
Die Verwendung dieser Autoklaven ist in verschiedenen Sektoren weit verbreitet, wie z. B. in der Automobilindustrie (hauptsächlich im Zusammenhang mit der Vulkanisation von Reifen), der Schiffbauindustrie (Herstellung von Fendern und Zubehör), der Konstruktion von Rollen und Förderbändern oder der Vulkanisation von Zusatzelementen (Rohre, Schläuche, Dichtungen usw.). Diese große Vielfalt an Märkten macht die Olmar-Autoklaven ATV für die Vulkanisation zu einer der gefragtesten Anlagen sowohl auf nationaler als auch auf internationaler Ebene.
Der gesamte Prozess läuft dank der neuen Software Olmar OCS, die vollständig von Ingenieuren von Olmar entwickelt wurde und die es ermöglicht, alle Variablen des Zyklus in Echtzeit zu kontrollieren, zu untersuchen und zu beeinflussen, vollautomatisch ab. Dieses moderne System garantiert ein optimales Endergebnis und ermöglicht darüber hinaus die Entwicklung verschiedener Arbeits-, Überwachungs- und Kontrollprogramme, die auf die unterschiedlichen Bedürfnisse jedes Kunden zugeschnitten sind.
- Industriebereiche
- Sonstige Autoklaven
Die Verwendung von vulkanisiertem Kautschuk in den technologisch fortschrittlichsten Industrien hat sich in den letzten Jahren verbreitet und sich von einer zufälligen Entdeckung zu einer beispiellosen Industrialisierung im Automobilsektor zu Beginn des 20. Jahrhunderts entwickelt.
Lassen Sie uns kurz seine Geschichte Revue passieren lassen: In einer Nacht im Jahr 1839 ließ Charles Goodyear Naturkautschuk, der mit Schwefel vermischt war, auf einer heißen Platte liegen; am nächsten Morgen hatte sich dieser Kautschuk in einen elastischen Gummi verwandelt, und damit war der erste Kautschukhärtungszyklus in der Geschichte vollzogen. Dieses Verfahren wurde 1843 von Herrn Goodyear patentiert (aber auch von Herrn Thomas Cook im Vereinigten Königreich, was zu verschiedenen Theorien über seine Erfindung führte).
Da Hitze und Schwefel mit dem Gott Vulcanus in Verbindung gebracht wurden, wurde dieses Verfahren Vulkanisation genannt.
Die Autoklav-Vulkanisation ist ein chemischer Prozess, der auf Kautschuk und andere natürliche Verbindungen mit Elastomereigenschaften angewendet wird und es ermöglicht, ihre Elastizität zu erhöhen und ihre Plastizität zu verringern, wodurch ihre mechanischen, physikalischen und Leistungsmerkmale wie Härte, Viskosität und Widerstandsfähigkeit (hauptsächlich gegen Zug und Witterungseinflüsse) verbessert werden.
Autoklaven für die Olmar-Vulkanisation (ATV) ermöglichen eine Beschleunigung dieser Prozesse, wodurch Naturkautschuk und Kunststoff (synthetischer Kautschuk) sicher und optimal in gehärtete Teile und Produkte umgewandelt werden können.
Der exponentielle Anstieg von in Autoklaven gehärtetem Kautschuk, der in unzähligen Sektoren und industriellen Prozessen Anwendung findet, ist hauptsächlich auf seine Verwendung in folgenden Bereichen zurückzuführen:
Produkte / Autoklav zur Vulkanisation von Kautschuk und Gummi / Autoklaven und Gummi und Kautschuk
- Beschichtung und Reparatur von Reifen für schwere Fahrzeuge wie Lastkraftwagen und Geländefahrzeuge (OTR – Off Road Tires)
- Beschichtung und Reparatur von Reifen für Personenkraftwagen (SBR – Styrol-Butadien-Kautschuk)
- Beschichtung von Förderbandrollen
- Beschichtung von Druckwalzen
- Herstellung von Gummidichtungen für die Automobil-, Luftfahrt- und Schifffahrtsindustrie, Kühlermanschetten, Kabel und Zündkerzenkappen (EPDM-Kautschuk)
- Elektrische Anwendungen wie die Isolierung von Hochspannungskabeln
- Beschichtung von Hochtemperaturkabeln
- Herstellung von Schläuchen und Gummimanschetten für niedrigen, mittleren und hohen Druck
- Herstellung von Gummischutzhüllen, bei denen die Wärmebeständigkeit gegenüber Ozon, Witterungseinflüssen, ätzenden Chemikalien oder Ölen wesentliche Eigenschaften sind
- Aushärten von Dichtungen und O-Ringen
- Sonstige wie Matten, Stiefel usw.
Diese durch das Autoklavverfahren verbesserten Produkte werden unter abrasiven Bedingungen und/oder in extrem korrosiven Umgebungen eingesetzt, wodurch ihre Lebensdauer verlängert und ihre Leistung verbessert wird. Dieses Ergebnis kann im Allgemeinen nicht durch ein standardmäßiges Formpressverfahren auf einer Presse erreicht werden.
Die von Olmar hergestellten Autoklaven für die Vulkanisation von Kautschuk (sogenannte „ATV“) zeichnen sich nicht nur durch ihren hohen technologischen Entwicklungsstand aus, sondern auch durch ihre Zuverlässigkeit und Langlebigkeit, die während ihrer gesamten Lebensdauer ein optimales Funktionieren und höchste Effizienz garantieren. Die Verwendung von Kautschuk in immer kritischeren Fertigungselementen hat zu einer exponentiellen Zunahme der Anforderungen an die Kontroll-, Ermüdungs- und Messprüfungen dieser Geräte geführt. Nur die fortschrittlichsten Autoklaven sind in der Lage, die von der Industrie geforderten Homogenitätsniveaus und Zyklen zu gewährleisten, weshalb Investitionen in Forschung und Entwicklung und deren ständige Verbesserung immer wichtiger werden.
In diesem Sinne widmet Olmar seit Beginn seiner Tätigkeit in diesem Sektor (das Unternehmen war in den 70er Jahren mehr als 15 Jahre lang Uniroyals Vertreter für Spanien) einen großen Teil seiner F&E-Ressourcen der Erforschung der Möglichkeiten dieser neuen Materialien und ist ein national und international führendes Unternehmen in deren Untersuchung und industrieller Anwendung.
Vulkanisationszyklus von Kautschuk
Wie bereits erwähnt, handelt es sich bei Kautschuk im Wesentlichen um ein Elastomer, das natürlichen oder synthetischen Ursprungs sein kann (in der Petrochemie durch chemische Synthese hergestellt) und anschließend in einem Autoklaven vulkanisiert wird, um seine physikalischen und strukturellen Eigenschaften zu verbessern.
In einem Standardzyklus muss der in den Autoklav eingeführte Kautschuk eine Temperatur von 170 °C (350 °F) und einen Druck von 6 bar Überdruck (90 psi) erreichen und eine vorgegebene Zeit lang bei dieser Temperatur und diesem Druck bleiben. Diese Bedingungen können je nach Kautschukart und Anwendung variieren.
Es ist wichtig, mit dem Lieferanten die maximale Zeit zu definieren, in der wir diese Temperatur- und Druckbedingungen erreichen wollen, um die von unserem Autoklaven erwartete Produktivität zu optimieren. Diese Daten sind für den Vergleich und die Abstimmung verschiedener Anlagen und die Auswahl der für unseren Prozess am besten geeigneten Anlage von entscheidender Bedeutung.
Die Vielfalt der für die Vulkanisation von Kautschuk existierenden Zyklen führt zu einer Vielzahl unterschiedlicher Autoklaven in Bezug auf:
Die von Olmar hergestellten Autoklaven für die Vulkanisation von Kautschuk (sogenannte „ATV“) zeichnen sich nicht nur durch ihren hohen technologischen Entwicklungsstand aus, sondern auch durch ihre Zuverlässigkeit und Langlebigkeit, die während ihrer gesamten Lebensdauer ein optimales Funktionieren und höchste Effizienz garantieren. Die Verwendung von Kautschuk in immer kritischeren Fertigungselementen hat zu einer exponentiellen Zunahme der Anforderungen an die Kontroll-, Ermüdungs- und Messprüfungen dieser Geräte geführt. Nur die fortschrittlichsten Autoklaven sind in der Lage, die von der Industrie geforderten Homogenitätsniveaus und Zyklen zu gewährleisten, weshalb Investitionen in Forschung und Entwicklung und deren ständige Verbesserung immer wichtiger werden.
In diesem Sinne widmet Olmar seit Beginn seiner Tätigkeit in diesem Sektor (das Unternehmen war in den 70er Jahren mehr als 15 Jahre lang Uniroyals Vertreter für Spanien) einen großen Teil seiner F&E-Ressourcen der Erforschung der Möglichkeiten dieser neuen Materialien und ist ein national und international führendes Unternehmen in deren Untersuchung und industrieller Anwendung.
- Abmessungen: Olmar bietet Autoklaven mit einem Nutzdurchmesser von 500 mm bis 10 000 mm und Längen von 1 000 mm bis 60 000 mm an.
- Maximale Arbeitstemperaturen und -drücke drücke (bis zu 482 °F) und 21 BarG (300 psi)
- Materialien: Kohlenstoffstahl, Edelstahl oder Kombination aus unterschiedlichen Materialien
- Anordnung: horizontal oder vertikal
Die üblichsten Phasen, die während eines Vulkanisationszyklus zu durchlaufen sind, sind folgende:
1 / Erhitzen und Druckbeaufschlagung
Die im Inneren des Autoklaven zu verwendenden Mittel zum Erhitzen und zur Druckbeaufschlagung sind von der Art des zu vulkanisierenden Kautschuks und seinem Verwendungszweck abhängig, wobei es vier Hauptmodalitäten gibt:
- Direkte Dampfbeheizung: durch die direkte Zufuhr von gesättigtem Dampf in die Autoklavenkammer (Olmar ist auch ein führender Hersteller von Dampfkesseln mit mehr als 1000 Referenzen weltweit und über 75 Jahren Erfahrung). Bei diesen Zyklen kann die Druckbeaufschlagung mit der Dampftemperatur korrelieren oder unabhängig davon durch die Zufuhr von Druckluft erfolgen.
- Indirekte Erwärmung durch Einleiten von Dampf oder Thermoöl: in einem Wärmetauscher im Inneren des Autoklaven, wobei die heiße Luft im Inneren durch eine Turbine und ihren Motor umgewälzt wird. In diesem Fall erfolgt die Druckbeaufschlagung unabhängig davon durch Einleiten von Druckluft in den Autoklaven. Durch die Verwendung von Heißluft anstelle von Dampf wird der direkte Kontakt des Kautschuks mit dem Dampf vermieden, wodurch die Feuchtigkeitsinfiltration minimiert und eine bessere Haftung des vulkanisierten Kautschuks erreicht wird.
- Indirekte Erwärmung durch elektrische Widerstände, wobei die Luft im Inneren des Autoklaven durch eine Turbine und deren Motor umgewälzt wird. In diesem Fall erfolgt die Druckbeaufschlagung unabhängig davon durch Einleiten von Druckluft in den Autoklaven. Durch die Verwendung von Heißluft anstelle von Dampf wird der direkte Kontakt des Kautschuks mit dem Dampf vermieden, wodurch die Feuchtigkeitsinfiltration minimiert und eine bessere Haftung des vulkanisierten Kautschuks erreicht wird.
- Gemischte Erhitzung mit direktem/indirektem Dampf: ein von Olmar entwickelter Autoklav, der es ermöglicht, je nach Bedarf jederzeit mit dem Besten aus beiden Technologien zu arbeiten.
2 / Stabilisierungsphase
Sobald diese Zielbedingungen (Arbeitstemperatur und -druck) erreicht sind, müssen wir sie während der Stabilisierungsphase, die dank des mit Siemens-SPS- oder Allen-Bradley-Technologie ausgestatteten OCS-Steuerungssystems (Olmar Control System) vollautomatisch erfolgt, für die festgelegte Mindestzeit aufrechterhalten.
3 / Abkühlung
Wie in der Aufheizphase hängen die im Inneren des Autoklaven zu verwendenden Kühl- und Druckentlastungsmittel von der Art des zu vulkanisierenden Kautschuks und seinem Verwendungszweck ab. Es gibt drei Hauptarten:
- Natürliche Kühlung: Der Druckkessel wird auf natürliche Weise gekühlt, indem der Dampf aus ihm entweicht. In einigen Fällen muss diese Druckentlastung durch Einleiten von Druckluft ausgeglichen werden, um eine optimale Produktqualität zu gewährleisten.
- Kühlung durch Dusche oder Sprühnebel: Der Druckkessel wird durch Wasser gekühlt, das von oben in den Druckkessel geleitet und durch eine Dusche oder einen Sprühnebel auf das Produkt gesprüht wird.
- Indirekte Kühlung: Dieses System basiert auf der Einleitung von kaltem Wasser in einen Wärmetauscher im Inneren des Autoklaven, wobei die Luft im Inneren des Geräts durch eine Turbine und ihren Motor umgewälzt wird.
Vulkanisationszyklen für Reifen
1 / Durch direkten Dampf
Nach dem Befüllen des Autoklavs wird der gesättigte Dampf unter Druck eingeleitet, wodurch die Reifen den programmierten Temperatur- und Druckbedingungen ausgesetzt werden.
2 / Durch indirekte Erwärmung
Bei diesem Zyklus wird jeder Reifen in eine Hülle (Kautschukmantel) gesteckt, die ihrerseits ein Ventil aufweist, durch das Druckluft zugeführt werden kann, um den Reifen zu pressen.
Sobald der Autoklav beladen ist, werden die Schläuche an die Hüllen angeschlossen, um sie während des Zyklus unter Druck zu setzen.
Wie bereits erläutert, wird die heiße Luft in diesem Fall durch die Rückführung von Dampf oder Thermoöl in einem Wärmetauscher oder auch durch elektrische Widerstände erzeugt. Wenn die Innentemperatur auf 125 °C (290 °F) ansteigt, werden die Hüllen, die die Reifen enthalten, aufgeblasen und Druck in den Autoklaven eingeleitet (mit einer Differenz von 2,1 BarG (30 psi)), bis die Kammer einen Druck von 5,5 BarG (80 psi) und die Reifen einen Druck von 8 BarG (115 psi) erreicht haben.
Zu diesem Zeitpunkt wird die Hülle, die den Reifen bedeckt, auf 4,2 bar (60 psi) unter Druck gesetzt; dieser Druck wird allgemein als „dritter Druck“ bezeichnet und garantiert eine optimale Haftung und eine bessere Endbearbeitung des Reifens.
Dieser Teil des Verfahrens dauert in der Regel etwa 120 bis 150 Minuten.
Nach Abschluss der vorstehenden Schritte wird der Druck in der folgenden Reihenfolge abgelassen:
- Dritter Druck
- Reifendruck
- Autoklavendruck
Der intelligente Autoklav, eine revolutionäre Steuerungssoftware
Präzision und Zuverlässigkeit sind grundlegende Faktoren bei der Glasherstellung. Aufgrund der hohen Anforderungen der Automobil- und Baubranche ist eine umfassende Überwachung und Kontrolle aller Prozesse im Autoklav erforderlich. In diesem Sinne hat Olmar die weltweit fortschrittlichste Software für Autoklaven zur Glaslaminierung entwickelt und damit seine Ziele der Digitalisierung und Effizienzsteigerung in den Herstellungsprozessen erreicht. Die neuen Autoklaven von Olmar sind intelligente Autoklaven, die in der Lage sind, die Druckbeaufschlagung mit Luft, die Heizrampen durch den Einsatz von elektrischen Batterien, Thermoöl oder Dampf, die Aufrechterhaltung der Vakuum-, Druck- und Temperaturwerte (Thermoelemente) während der Aushärtung sowie das anschließende Abkühlen und Druckentlasten automatisch zu steuern und so die Kontrolle und Parametrierung jeder einzelnen Herstellungsphase zu ermöglichen. Dadurch können wir ein vollkommen transparentes Glas mit optimalen PVB-Überlauf- und Schrumpfungsparametern erzielen, die stets den höchsten Marktstandards entsprechen.
Nicht nur die Kontrolle und Analyse dieser Werte (Druck, Vakuum oder Temperatur) während des Zyklus, sondern auch nach dem Zyklus ist wichtig. Dank der Auswertung aller während des Prozesses im Autoklaven gesammelten Daten ist es möglich, mögliche Verbesserungspunkte zu erkennen und den Zyklus maximal zu optimieren. Durch ein vollständig von der Firma über ihre Elektro- und Softwareabteilungen entwickelten Kontrollsystems bietet Olmar seinen Kunden optimierte Leistungen und durch seine innovative Berichtstechnologie die genaueste Datenkontrolle und -analyse auf dem internationalen Markt. Damit setzt das Unternehmen auf die Entwicklung der sogenannten „Industrie 4.0“ und wendet alle verfügbaren Innovationen in seinen Autoklaven an.
Olmar hat sich auf die Entwicklung eines „intelligenten“ Autoklaven konzentriert und dabei den Schwerpunkt auf Energieeffizienz, Benutzerfreundlichkeit, vorausschauende Steuerung und geringen Wartungsaufwand gelegt.
Die OCS-Steuerungssoftware integriert alle diese Funktionen, reduziert den Verbrauchskosten des Autoklaven, verbessert seine Produktivität und optimiert alle regelmäßigen Wartungsarbeiten. Dank seiner hohen Konnektivität und der Integration der fortschrittlichsten Lösungen für die Fernverbindung bietet unser technischer Service erstklassigen Support in jedem Land der Welt.
All dies ist in eine solide Unternehmensstruktur eingebettet, die familiär geprägt und gleichzeitig flexibel und agil ist und in der Lage ist, den gesamten Herstellungsprozess „inhouse“ durchzuführen; ein Unternehmen, das sich auf die kontinuierliche Suche nach Innovation und Wachstum konzentriert. Dies zeigt sich in seiner neuen Abteilung „Additive Kaltumformung“, einem revolutionären Konzept, das aus unserer Investition in Forschung und Entwicklung hervorgegangen ist.
Dampferzeuger von Olmar
Olmar ist heute weltweit führend in der Herstellung von Autoklaven für Kautschuk. Diese Führungsposition beruht hauptsächlich auf der Kombination aus traditioneller und innovativer Technik und einer umfassenden Kenntnis sowohl des Autoklaven als auch des Verfahrens.
In diesem Bereich hat Olmar außerdem einen wichtigen Vorteil gegenüber seinen Wettbewerbern: sein Wissen und seine Produktionskapazität in Bezug auf Dampferzeuger mit mehr als 1000 Referenzen und 50 Jahren Geschichte.
In diesem Zusammenhang empfehlen wir Ihnen, unseren Abschnitt „Dampferzeuger“ zu besuchen, in dem Sie die verschiedenen von uns hergestellten Kesselreihen mit Leistungen von 100 kg/h bis 30 000 kg/h finden.
Darüber hinaus kann Olmar seinen Kunden optional eine schlüsselfertige Lösung anbieten, die alle Hilfssysteme umfasst, die den Autoklav/Dampferzeuger für das Vulkanisieren von Kautschuk ergänzen:
- Manuelle, halbautomatische oder automatische Ladesysteme.
- Schalldämpfer für geringe Geräuschemissionen während der Druckentlastung.
- Hardware und Sensoren zur Prozessüberwachung.
Die Möglichkeit, sowohl für den Autoklav als auch für seine Zusatzausrüstung einen einzigen Lieferanten auszuwählen, erleichtert die Kommunikation und die Integration aller Komponenten und erhöht die Wahrscheinlichkeit eines erfolgreichen Endergebnisses des Projekts.
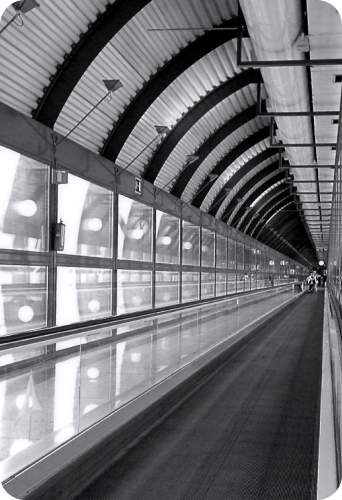
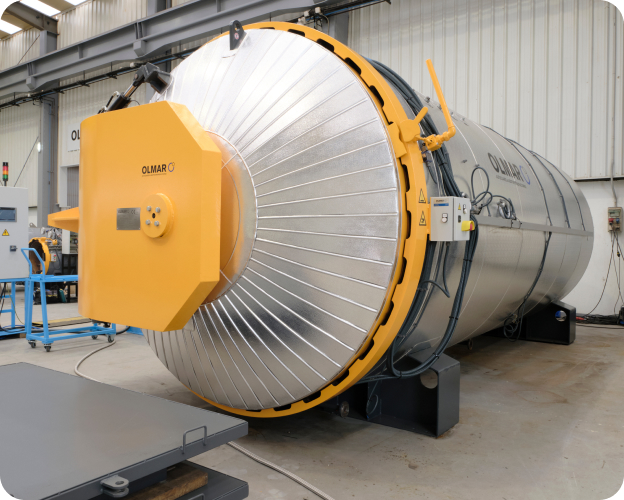
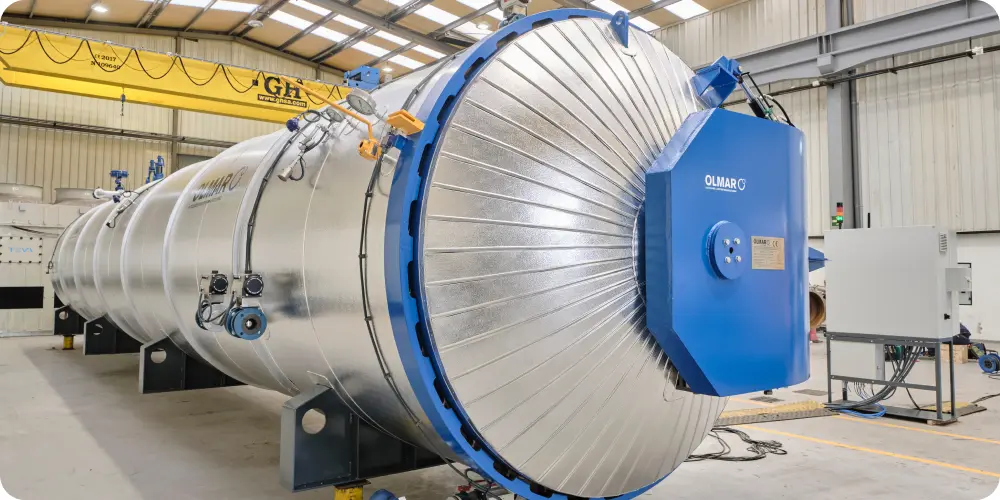
Schwere Nutzfahrzeuge und Personenkraftwagen in der Automobilindustrie: Hauptsektor für den Einsatz von Autoklaven für die Vulkanisation von Kautschuk
Die Erfahrung des Unternehmens, die durch Tausende von internationalen Referenzen und erstklassigen Kunden bestätigt wird, hat sich im Laufe der Jahre auf der Grundlage von Werten wie Exzellenz, Anstrengung und ständiger Innovation weiterentwickelt. Führende Unternehmen wie Michelin, Bridgestone, Continental, Siemens oder Hutchinson und viele andere haben sich bei der Entwicklung einiger ihrer wichtigsten Projekte auf die Autoklaven von Olmar verlassen, um Produkte zu entwickeln, die die fortschrittlichsten Lösungen für die Automobilindustrie, die Elektrizitätswirtschaft usw. bieten. Ein Beweis dafür sind die zahlreichen Prozesse, bei denen Olmar-Autoklaven und -Kontrollsysteme eingesetzt und integriert werden.
Olmar ist in all diesen Bereichen präsent und beteiligt sich aktiv an aktuellen und bahnbrechenden Projekten, die unsere Zukunft verändern werden, indem es sich mit Engagement, Exzellenz und Innovation für technologische Lösungen zur Herstellung von Autoklaven für die Vulkanisation von Kautschuk einsetzt, die es bisher noch nicht gab. Unsere Steuerungssoftware OCS, die derzeit als die fortschrittlichste Anwendung für die Kautschukbearbeitung gilt, macht Olmar zu einem internationalen Referenzunternehmen in einem zunehmend wettbewerbsorientierten Weltmarkt.
Der Anstieg des Reifenverbrauchs und der Reifenproduktion sind zweifellos Aufwärtstrends, die einen Markt definieren, auf dem die Einzelumsätze der großen Unternehmen 20 Milliarden Euro übersteigen.
Olmar ist heute ein zuverlässiger Partner, um diese Herausforderung in jedem Land der Welt zu bewältigen.
Weltweite Präsenz
Die Präsenz von mehr als 1500 Olmar-Autoklaven in 150 Ländern ist heute eine Erfolgsgeschichte und ein Erbe, das von Generation zu Generation weitergegeben wird (heute ist Olmar ein Familienunternehmen in vierter Generation).
All dies wird von den neuesten internationalen Zertifizierungen sowohl auf der Ebene der Herstellung als auch der Verfahren und der Qualität begleitet, wobei unter anderem die CE-Kennzeichnung (Europa), ASME (Amerika und Asien), SELO (China), JIS (Japan) usw. vorhanden sind.
Die Zukunft, eine neue Generation von Autoklaven
In diesem vielversprechenden Szenario des Wachstums und der neuen Herausforderungen festigt sich Olmar als weltweit führendes Unternehmen und präsentiert seine Geräte und technologischen Lösungen als Garantie für höchste Qualität und Effizienz, um den Herausforderungen der Industrie in den kommenden Jahren zu begegnen. Dank der in ihrer über 75-jährigen Geschichte gesammelten Erfahrung und eines Teams hochqualifizierter Experten stellt sich das Unternehmen diesen neuen Herausforderungen mit der Sicherheit
und Zuversicht, die erforderlich sind, um den Bedürfnissen seiner Kunden auf der ganzen Welt gerecht zu werden.
All dies wird von den neuesten internationalen Zertifizierungen sowohl auf der Ebene der Herstellung als auch der Verfahren und der Qualität begleitet, wobei unter anderem die CE-Kennzeichnung (Europa), ASME (Amerika und Asien), SELO (China), JIS (Japan) usw. vorhanden sind.