Glass autoclaves
Olmar ATG glass lamination autoclaves are a world leader in sectors such as the automotive and construction sectors, where they are used to manufacture laminated glass windscreens and polyvinyl butyral (PVB) resins and to develop all types of laminates for buildings and other architectural solutions.
- Industries
- Other Autoclaves
These autoclaves have the latest technology to fully control the process. Glass is laminated by heating the air inside the autoclave, either by means of electrical resistors or with a steam/thermal oil exchanger. The hot air is distributed evenly by an electric fan, so that maximum temperature homogeneity is achieved in all areas. Similarly, a water coil is responsible for cooling the environment at the end of the cycle with the aim of lowering the temperature to the desired value and achieving an optimum end result.
Olmar has developed new heat soak test (HST) ovens to complement these autoclaves, which make it possible to carry out breakage tests on tempered glass sheets in accordance with the guidelines set out in current legislation.
The use of glass in the most technologically advanced projects has become widespread over the last few years, moving from being almost handcrafted to unprecedented industrialisation. With applications in a myriad of projects and industrial processes, the exponential growth in the use of laminated glass has been driven by five main factors:
SAFETY/SECURITY
A key element since the early days of the laminated glass industry, particularly in the manufacture of windscreens for the automotive sector.
CREATIVITY
Increasing use in design and architecture. An industry that needs technologically advanced glass to deliver in ways that were unimaginable 20 years ago.
DIGITALISATION
Mediante la creación de vidrios interactivos, capaces de ofrecer multitud de funciones aplicables tanto en el mercado automovilístico como en usos domésticos o empresariales de todo tipo.
A STRUCTURAL ELEMENT
Its use as a structural element has made laminated glass a central, essential element in the construction of any building. This demand has in turn increased the international presence of Olmar autoclaves, making it a leading supplier in the sector.
ENERGY EFFICIENCY
By means of intelligent laminated glass, which can absorb sunlight or darken automatically, depending on outside light conditions. These functions, which are already available in cars and buildings, make it possible to optimise air conditioning systems with a positive impact on the environment and a significant reduction in CO2 emissions.
Since it started its activity in this sector, Olmar has dedicated a large part of its resources and R&D to researching the possibilities of these new materials, and has become a national and international benchmark in their study and industrial application.
Los autoclaves para laminado de vidrio fabricados por Olmar (denominados “ATG”) destacan no sólo por su alto nivel de desarrollo tecnológico, sino por su fiabilidad y durabilidad, que garantizan el mejor funcionamiento y los mayores niveles de eficiencia durante toda su vida útil. La aplicación del vidrio en elementos de fabricación cada vez más críticos ha traído consigo un aumento exponencial en la exigencia de los test de control, fatiga y medida de estos equipos. Sólo los autoclaves más avanzados son capaces de garantizar los niveles de homogeneidad y los ciclos demandados por la industria, por lo que resulta cada vez más importante la inversión en I+D y la constante mejora de los mismos.
Cycle for laminated glass in an autoclave
As we have already seen, laminated glass is essentially a type of safety glass that is made by joining two or more panes of glass of varying thickness, placing one or more layers of polyvinyl butyral (PVB) between them and putting them in an autoclave.
In a standard cycle, once the glass has been put into the autoclave, it must reach a temperature of 140ºC (280ºF) and a pressure of 12.5 BarG (180 psig), and stay in these conditions for a minimum of 30 minutes. These conditions may vary depending on the thickness and number of glass panes.
It is essential to correctly define the maximum time in which these temperature and pressure conditions need to be reached with the supplier, thereby optimising the productivity we expect from our autoclave. The data given below are a good way of comparing and aligning different autoclave offers
- Heating ramp rate: we recommend a heating ramp rate of 2°C/min as a starting point (a standardised value in the glass industry), which would make it possible to raise the temperature from 20°C to 140°C in 60 minutes. In order to reduce their prices, some suppliers will offer ramp rates of 1°C/min, thereby limiting the capabilities of their equipment and their cost-effectiveness (cycles will last twice as long or allow half the load).
-
Cooling ramp rate: we recommend a cooling ramp rate of 2°C/min as a starting point (a standardised value in the industry), which would make it possible to lower the temperature from 140°C to 60°C in 40 minutes. If you intend to work with Sentryglas (https://innovationaward.trosifol.com/ventajas-de-sentryglas/?lang=es), the minimum cooling ramp rate should be 2.2°C/min. Olmar supplies ‘”compact cooling systems” as an option, which can include different configurations:
· Cooling tower
· Dry cooler
· Chiller
· Plate heat exchanger
All this allows us to offer a “turnkey” solution. - Pressurisation ramp rate: the maximum time to reach the working pressure of 12.5 barg (180 psig) will depend on the time defined for the heat ramp rate. Therefore, if we have defined a ramp of 2ºC/min to go from 20ºC to 140ºC, we will need a maximum time of 60 minutes to reach that pressure. Olmar works with world-class compressor suppliers (Kaeser, Atlas Copco, etc.) to provide a “turnkey” solution.
- Pressurisation ramp rate: This ramp rate defines the time it takes to go from working pressure (12.5 barg (180 psig)) to atmospheric pressure. Olmar recommends a ramp rate of 0.7 barg/min. Olmar offers a “silencer” which has been calculated and designed for these conditions, in order to keep within the maximum authorised noise level.
/ Motors at the top /
Autoclave with vertical airflow
Olmar offers an innovative design for long autoclaves or continuous production lines for laminating windscreens for cars or buses, with a vertical airflow and motors at the top that allow for an optimal, even distribution of air inside the autoclave.
This configuration makes it possible to manufacture an autoclave with two doors, loading the glass through the main inlet (door 1) and removing it as 100% laminated glass through the other end of the autoclave (door 2).
This double door configuration means a slight increase in the diameter of the autoclave which in turn means a continuous flow of glass being loaded, a reduction in time and therefore, greater productivity.
/ Fire safety /
Autoclave cleaning cycle
Olmar autoclaves are supplied with OCS software that includes a high-performance cleaning cycle to prevent potential fires during a cycle. This is a fully automated process.
Heat soak test (HST) in the autoclave
The technology developed by Olmar makes it possible to carry out heat soak test cycles in the same autoclave in which glass lamination cycles are carried out.
The heat soak test (HST) process minimises the risk of spontaneous breakage caused by nickel sulphide particles by subjecting the tempered glass to extremely adverse conditions. This eliminates the risk of spontaneous breakage in tempered glass for outdoor use, which is generally difficult to replace.
European standard EN-14179-1, which regulates the correct way to apply the heat soak test, stipulates that the heat soak cycle consists of three phases:
- A heating phase: where all of the glass goes from room temperature to 280ºC.
- A maintenance phase: all of the glass is kept at 290ºC +- 10ºC for 2 hours.
- A cooling phase: once the maintenance phase has been completed, the temperature of the glass is brought back down to room temperature.
The intelligent autoclave - revolutionary control software
Precision and reliability are key factors in the glass manufacturing process. All of the processes that take place inside the autoclave must be closely monitored and controlled due to the high levels of demand in the automotive and construction sectors. In this sense, Olmar has developed the most advanced software in the world for autoclaves for laminating glass, thereby fulfilling its objectives of digitalisation and efficiency in manufacturing processes. New Olmar autoclaves are, in short, intelligent autoclaves capable of automatically controlling the pressurisation with air, the heating ramp rates of these fluids using electric batteries, thermal oil or steam, the maintenance of vacuum, pressure and temperature values (thermocouples) during curing, and the subsequent cooling and depressurisation, thereby making it possible to control and configure each of their phases. All of this makes it possible for us to produce completely transparent glass, with optimum PVB creep and relaxation parameters that are always in line with the most demanding market standards.
It is not only important to monitor and analyse these values (pressure, vacuum and temperature) during the cycle, but also after the cycle. It is possible to identify potential areas for improvement and optimise the cycle as far as possible by studying all the data collected during the process carried out inside the autoclave. By means of a control system, which was fully developed by the company’s electrical and software departments, Olmar is able to offer its customers optimised performance and, through its innovative reporting technology, the most accurate control and data analysis system on the international market, making a firm commitment to developing the so-called ‘Industry 4.0’ and applying all of the innovative features available in its autoclaves.
Olmar has focused its efforts on creating an “intelligent” autoclave, concentrating its efforts in the fields of energy efficiency, usability, predictive control and low maintenance.
Its OCS control software integrates all of these features, thereby reducing the autoclave’s consumption costs, improving its productivity and optimising any periodic maintenance tasks that need to be carried out. Our technical service provides first class support in any country in the world, thanks to its high degree of connectivity and the incorporation of the most advanced remote connection solutions.
All of this has been embraced in a solid business structure, with a family tradition, yet at the same time flexible and agile, capable of carrying out the entire manufacturing process “in house”; a company focused on a continuous search for innovation and growth. This is demonstrated by its new ‘’cold additive technology‘’ division, a revolutionary concept stemming from our investment in R&D.
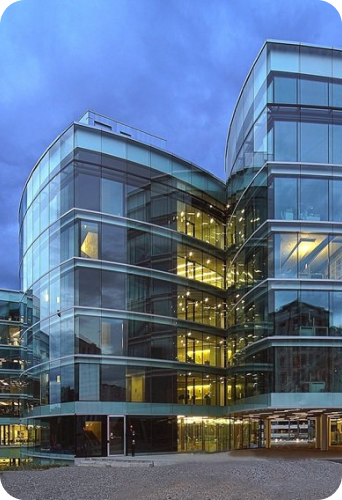
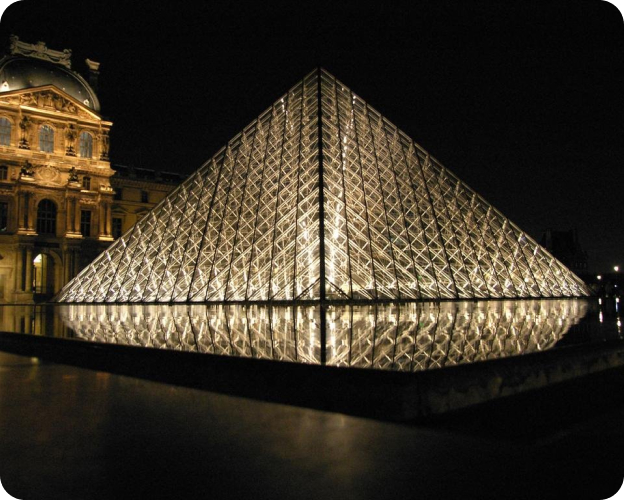
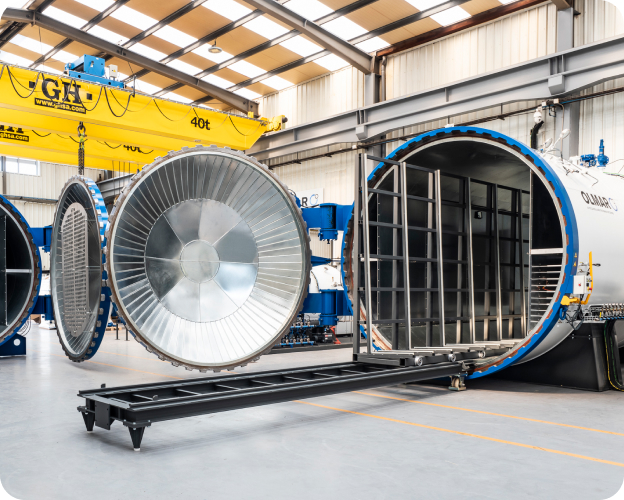
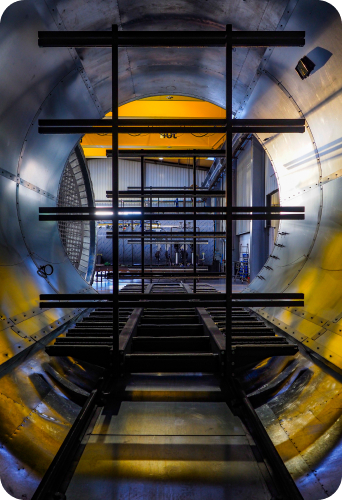
CFX and CFD studies based on finite elements
Olmar carries out homogeneity studies using ANSYS CFX and CFD (computational fluid dynamics) software, based on finite elements.
This analysis of the structural behaviour, homogeneity of the temperature and speeds inside the autoclave has demonstrated that both the mechanical configuration chosen for air recirculation and the heating/cooling systems selected optimise the glass lamination process in autoclaves.
Vacuum systems and auxiliary equipment | Slides, cooling systems and compressors
Olmar is one of the world’s leading manufacturers of glass lamination autoclaves, based on a combination of traditional and innovative engineering and a deep knowledge of both autoclaves and the processes involved.
In this sense, Olmar is able to offer its customers the option of a “turnkey” solution that includes all of the auxiliary systems that complement the glass lamination autoclave:
- An automatic vacuum system consisting of a lubricated rotary vane vacuum pump and a number of inlets selected by the customer based on the number of glass panes to be laminated in a vacuum bag.
- Manual, semi-automatic or automatic loading systems.
- Cooling systems using our compact solution, fitted with a cooling tower, dry cooler, chiller, heat exchanger or a combination of these.
- State-of-the-art compressors made by Kaeser, Atlas Copco or similar.
- Silencer for low noise emissions during depressurisation.
- Hardware and sensors for monitoring processes.
The possibility of selecting a single supplier, both for the autoclave and its auxiliary equipment, makes it easier to communicate about and integrate all of them, and increases the likelihood of success in the end result of the project.
Hinged and davit arm doors
Olmar offers two door opening alternatives, depending on the design properties of each autoclave:
In this sense, Olmar is able to offer its customers the option of a “turnkey” solution that includes all of the auxiliary systems that complement the glass lamination autoclave:
- A hinged door opening.
- A davit arm door opening.
The choice of one option or another will depend on the diameter of the autoclave, the customer’s preference and the space available. The autoclave can be operated by a hydraulic or pneumatic system and can be manual, semi-automatic or fully automatic.
International certification
Olmar has all of the manufacturing, procedural and quality certification required, with CE (Europe), ASME (America and Asia), SELO (China), CU TR (Russia), JIS (Japan), etc certifications, among others.
The company’s Quality Department is responsible for ensuring that all of the processes related to the equipment we manufacture comply with the regulations and requirements of each country to guarantee the highest levels of quality at all times.
Automotive and construction sectors: the main sectors that use glass autoclaves
The company’s experience, backed by thousands of international references and top tier customers, has grown over the years based on values such as excellence, effort and constant innovation. Leading companies such as AGC, Saint-Gobain Glass and Sekurit, Vitro and AGP, among many others, have put their trust in Olmar autoclaves to undertake some of their most important projects, with products that provide the most advanced solutions for sectors such as architecture, construction and the automotive industry. Proof of this is the large number of processes in which Olmar autoclaves and control systems are used and have been integrated.
As a result, a very wide range of products, from the simplicity of small glassware items for the home to windscreens for cars and buses and smart, interactive glass that will soon be a part of our everyday lives. A host of options now make it possible to manufacture complex laminated glass in sizes and shapes that would have been unimaginable just 10 years ago.
Olmar is involved in all of them, actively taking part in current, disruptive projects that will change our future, bringing effort, excellence and innovation to technological solutions for manufacturing glass lamination autoclaves that have never been seen before. Our OCS control software, which is currently considered to be the most advanced application for treating glass, has made Olmar a point of reference internationally in an increasingly competitive world market.
In short, the increase in consumption and production of laminated glass has become a reality, with a turnover that is about to exceed 40 billion euros in sales.
Olmar is a trusted partner for this challenge in any country in the world today.
The future - a new generation of autoclaves
The presence of more than 1500 Olmar autoclaves in 150 countries is a success story and a legacy that has been passed down from generation to generation. As a 4th generation family company, Olmar has consolidated its position as a world leader, presenting its equipment and technological solutions as a guarantee of the highest quality and efficiency when it comes to tackling the industry’s challenges in the coming years.
Thanks to the experience acquired over its 75-year history and a team of highly qualified technical experts, the company is looking to tackle these new challenges with the security and confidence necessary to respond to the needs of its customers all over the world.